YKMBⅡ PRINTER
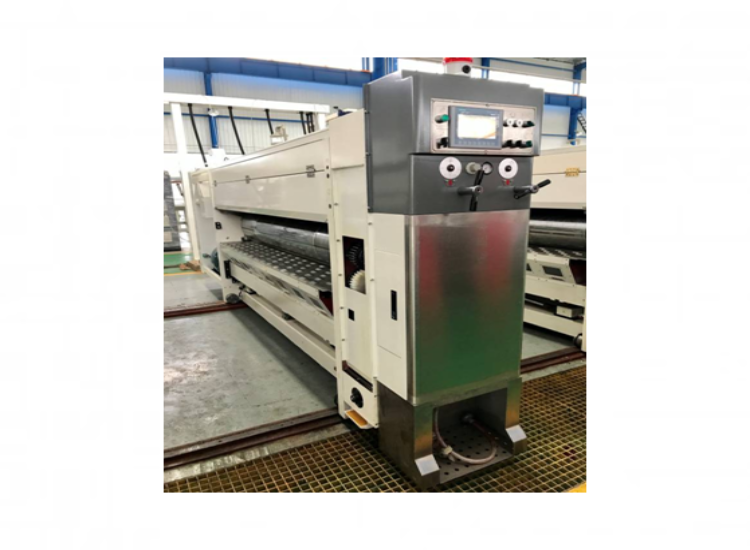
About Me
The YKMBⅡ Printer, manufactured by J.S. Machine, is a high-performance printing solution specifically designed for the packaging industry. This advanced printer is known for its precision and versatility, capable of handling various substrates used in corrugated packaging. Engineered with state-of-the-art technology, the YKMBⅡ offers exceptional print clarity and vibrant color reproduction, making it ideal for branding and detailed graphic requirements on packaging materials.One of the key features of the YKMBⅡ Printer is its user-friendly interface, which allows operators to easily set up and adjust print specifications, maximizing productivity and minimizing downtime.
Panel size: Feeding unit (one unit)
- No-pressure servo lead edge feeder as standard configuration or Sun-Automation Lead-edge feeder as option.
- No-pressure feeding ensures the sheet strength, manual feeding gap adjustment via self-locking gear box with dials readout. Sun-Automation feeder with tandem feed rolls mechanism with dual-rubber wrapped.
- Sheet cleaner with two-row brushes and dust-removal blower, removing contaminants before printing.
- Assistance suction feeding device
- Motorized adjustment for side guide with double control ways, touch screen and button control. Manual link-adjustment for feed gate.
- Backstop manual adjustment as standard, motorized adjustment is available.
- Touch screen control and automatic zero-reset device One air compressor
Printing unit (one units)
- Steel anilox roll (180~280LPI) , Ceramic anilox roll (180-550LPI) (option)
- Rubber roll ink metering system, or Doctor-blade ink metering system (option)
- Planetary gearing mechanism for easy register adjustment CW or CCW within 360 degreewith double control ways, touch screen and button control.
- Motorized register adjustment with inverter motor and enable functions of clear memory and return to zero automatically.
- Motorized printing cylinder lateral shifting mechanism with double control ways, touch screen and button control.
- Manual gap adjustment via self-locking gear box with dials readout. such as gap between rubber roll and anilox roll, gap between anilox roll and printing cylinder, gap between upper pull roll and lower one, gap between printing cylinder and impression roll.
- Roll transferring system, or vacuum suction sheet transferring system (option)
- Touch screen control with zero-return device.
- Low ink level alarm device, automatic ink-washing system.
Slotting unit (one unit)
- Brake speed-reducing motor for slotting registration and case height adjustment with frequency-converter control. Double control ways, touch screen and button control.
- Motorized slotting space, pre-scoring space and scoring space link-adjustment with double control ways, touch screen and button control.
- Manual gap adjustment via self-locking gear box with dials readout. such as slotting gap, pre-scoring gap and scoring gap
- Touch screen control and automatic zero-reset device
- Equipped with two sets of hand hole cutting attachment.
Die-cutting unit (one unit)
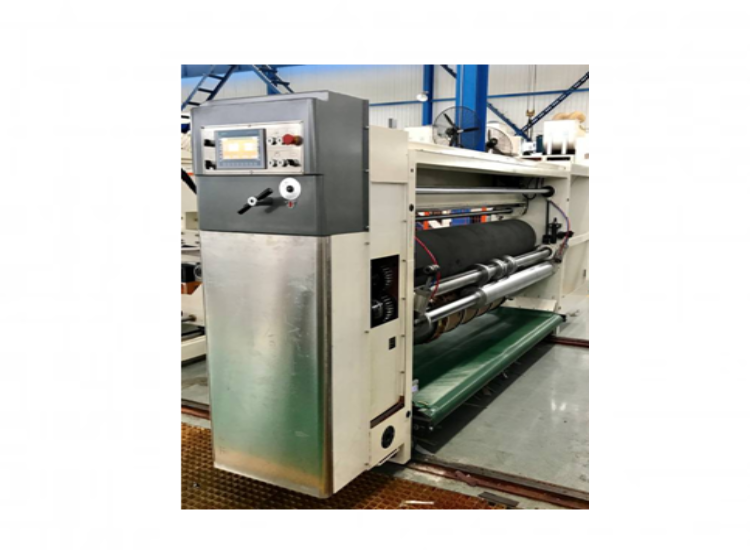
- Motorized die-cutting register adjustment by inverter motor with double control ways, touch screen and button control.
- Motorized die-cutting gap adjustment and manual conveying gap adjustment via self-locking gear box with dials readout.
- Steel die roll with surface hard chrome plating and inserting holes with thread.
- Steel anvil roll, surface hard chrome plating, equipped with CUE anvil cover from USA. Axial automatic movement range of±20mm. Automatic speed tracing benefits to prolong the lifetime of anvil cover and improves the die-cutting precision.
- Equipped with anvil blanket-leveling mechanism.
- Equipped with motorized waste removing device.
Stacking unit (one unit)
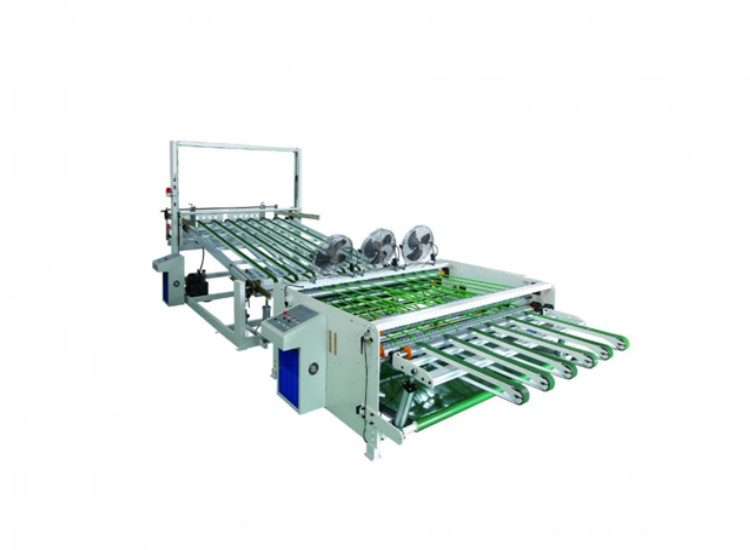
- Front section is pneumatic controlled for collecting sheet, the back section is hydraulic lifting with aluminum structure for convenient adjusting and safety.
- Maximum stacking height: 1600mm
- Manual button control and automatic control for lifting bed
- Equipped with transverse waste removing device.
Order management system
Folding unit
- Motorized brush wheel and high-pressure blower to remove corner-cutting scraps.
- Vacuum belt transfer with less wear and high feeding accuracy.
- Automatic air cylinder adjustment for belt tension control, automatic belt loosening when power off prolongs belt lifespan.
- Synchronous transfer of top and bottom high friction needle belt in front section ensures square feeding.
- Auxiliary folding wheel for 2nd time creasing, ensures better formation for 5 ply carton.
- Folding wheels in rear section effectively control sheet folding process and avoid fishtail.
- Accurate speed differential adjustment for top and bottom folding belts reduces scissors error when the carton is formed. Motorized folding beam movement for different carton sizes demand
Feeding unit
Feeding system:
- SUN lead edge feeder, taking sheet's leading edge as positioning benchmark, in line with printing, slotting and die-cutting positioning benchmark.
- Equipped with servo main drive motor.
- Back suction conveying to improve the feeding precision.
- Extend feeding function helps feeding low quality sheets (automatic adjustment of extension stroke).
- Air volume controlled by frequency converter (stepless adjustment) ensures accuracy and easy adjustment.
- Suction range adjusts to sheet width (attached is suction force tested by negative pressure meter).
- Return to zero detection.
- Dust removal system:
- Brush dust removal system, mechanically remove dust on printing surface.
- Electrostatic removal system, remove dust and reduce its adsorption capacity.
- Suction dust removal system to absorb dust through negative pressure cavity.
- Sticky roll dust removal system, transplant offset printing technology, cohesive rubber roll to get rid of remained dust after previous three dust-removal processes.
- Side guides and baffle:
- Motorized adjustment and value input on touch screen adjustment of front damper gap, manual adjustment in transverse position, manual adjustment of front damper height difference at both ends.
- Motorized adjustment and value input on touch screen adjustment of side guides position, dual protection of maximum and minimum limit position through program and limit switch. Side guides can be adjusted individually. Side guides jogging device at drive side with 150mm stroke.
- Motorized adjustment and value input on touch screen adjustment of backstop (sheet width) position, dual protection of maximum and minimum limit position through program and limit switch, sheet separating device effectively share accumulated weight from upper sheets to ensure feeding accuracy of sheets with variable speed and specification. In addition, auxiliary roller support bar prevents large size sheets from sagging.
- Feeding roll:
- Motorized adjustment and value input on touch screen adjustment of gap; maximum and minimum limit position protected by program.
- Knurled, ground and chrome coated lower roll, and upper roll is slotted and coated with rubber. (rubber hardness 20°~35°).
- Sheet-counting device (5 digits adjustable).
- Sheet width 1000mm and warped by 20mm can also be fed smoothly.
- Fault location display device is integrated with diagnosis function.
- Function of single sheet feeding and emergency stop device.
- Skip feeding device.
- Touch screen to display running speed and quantity.
Printing unit
- Motorized adjustment and value input on touch screen adjustment of printing size and gap, fine tuning accuracy to 0.1mm.
- Vacuum transfer with ceramic wheel.
- Printing cylinder:
- Increased anilox roll quick-change device for various colors to improve equipment adaptability.
- Can be equipped with special tooling to quickly change the anilox roll (about 10 minutes per roll change).
- Memorize and return to initial position function for easy cleaning and mounting of printing plate, program can save relative position of each printing unit before machine stop and automatically reset with accuracy +/-0.1mm.
- Non-stop printing plate change: Printing plate and color can be changed when current unit is stop while machine is running; equipped with safety division plate.
- Motorized adjustment and value input on touch screen adjustment of transverse position with 10mm stroke for left and right direction respectively.
- Surface ground and chrome-coated, marked center line for plate mounting.
- Dynamic balance accuracy G1.0.
- Automatic variable speed adjustment of registration, accurate positioning and time saving, three operating modes, i.e. value setting, button quantified, inching continuous operation.
- Plate-mounting device: fixed single slot type, plate size: 980mm, origin 100mm.
- Inking system:
- 60°angle cellular ceramic anilox roll, dynamic balancing calibration, easy assembling and disassembling structure (roll change time≤20min./unit). 5 sets of ceramic anilox roller 250 ~ 750LPI (LPI is customized)
- Motorized adjustment and value input on touch screen adjustment of gap between anilox roll and printing cylinder (plate), with fine tuning accuracy to 0.03mm.
- Three-position knob for automatic, manual and stop of inking.
- Equipped with automatic sequential inking function: linked with feeding button, sequential inking for printing units, delay time can be set individually.
- Light is on while inking.
- Ink supply system:
- Chamber doctor blade system for printing units, cohere resistant filming coated on chamber. Equipped with high-pressure water cleaning, the blade gap can be adjusted to control the amount of ink
- Peristaltic pump accurately controls the amount of ink, and the dual pump heads supply ink smoothly without bubbling
- Ink bucket and peristaltic pump plug design for easy operation and maintenance
- Deep ink-saving technology: The ink channel surface is ink free treatment (Teflon coating) plus program ink saving, single-color single-wash ink loss ~ 600cc.
- Doctor blade is made of polymer plastics.
- Low ink alarm.
- Ink supply and ink recycling pipe can be pneumatically switched place for convenient cleaning (no need to move the bucket), waste water centralized recycling to ensure clean on the machine.
- Automatic ink recycling and cleaning, cleaning can be finished within 3 minutes.
- Impressing system:
- Knurled steel impressing roll with dynamic balancing calibration.
- Motorized adjustment and value input on touch screen adjustment of gap, dual protection for top and bottom limit position through program and limit switch.
- Printing cylinder can move upward and downward by 130mm in total. Impressing roll will not go up and down.
- Each unit are equipped with return device.
- Printing precision: ±0.3mm.
Conveying system
- Vacuum transfer with ceramic rollers.
- Equipped with passway.
Creasing unit
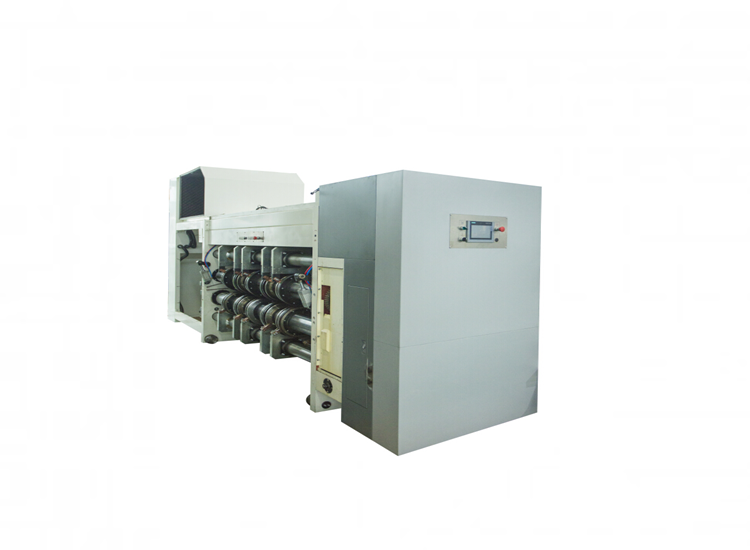
- Independent creasing unit, flexible and convenient adjustment
- Equal-diameter large pre-creasing and creasing wheel, the creasing wheel and the printing cylinder at the same speed, to ensure the straightness of the pressure line, but also avoid ink drag phenomenon at full size printing.
- Equipped with two types of blade, adapted to different thickness and quality requirements of paperboard creasing.
- Motorized adjustment and value input on touch screen adjustment of gap and creasing relative parameters with accuracy to 0.1mm.
- Ten-axis structure: conveying---pre-creasing 1---pre-creasing 2—creasing—conveying, adopts quick change creasing adhesive tape structure; motorized adjustment and value input on touch screen adjustment of five groups of gaps.
- Top and bottom pre-creasing axis, creasing axis, feeding axis and feeding roll are ground and hard chrome coated steel rolls.
- Gap between pre-creasing wheel and creasing wheel is driven by high precision gear box, together with motorized adjustment and value input on touch screen adjustment, engaged in order change, anti-collision design for mechanical part and limit switch, equipped with calibrated scale.
Slotting unit
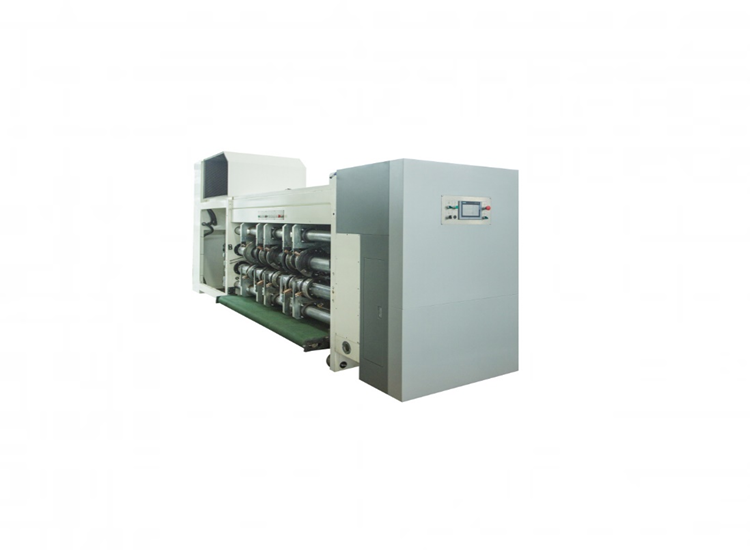
- Dual slotting structure, no case-height limit.
- Independent servo drive, die-cutting register automatic positioning
- Motorized adjustment and value input on touch screen adjustment of slotting relative dimension and gap, with fine tuning accuracy to 0.1mm.
- Eight-axis structure: conveying--slotting--conveying--slotting, dual slotting structure; motorized adjustment and value input on touch screen adjustment of four groups of gaps.
- Top and bottom slotting axis, creasing axis, feeding axis and feeding roll are ground and hard chrome coated steel rolls.
- Gap between slotting blades is driven by high precision gear box, together with motorized adjustment and value input on touch screen adjustment, engaged in order change, anti-collision design for mechanical part and limit switch, equipped with calibrated scale.
- Saw-tooth slotting blades with arc length260 mm, which also can be customized.
- Slotting blade holder equipped with wear-resisting plate, which is made of refining tool steel, can reduce wearing of toggle block and maintain alignment accuracy between top and bottom slotting blade, thus to prolong slotting blades lifespan.
- Motorized adjustment and value input on touch screen adjustment of registration and case height, engaged in order change.
- Fixed middle slotting carriage (motorized numerical control is optional)
- Top corner-cutting blade with flexible structure, equipped with rigid sliding corner-cutting anvil.
- Equipped with motorized belt waste removal device.
- Pneumatic locking with creasing unit, and it can be separated apart by 1000mm, easy for maintenance and blade change.
- Slotting accuracy: ±1.0mm
Die-cutting unit
- Motorized adjustment and value input on touch screen adjustment of die-cutting relative dimension and gap, with fine tuning accuracy to 0.1mm.
- Servo drive isolates impact to printing from die-cutting.
- Tungsten-plated spiral roller screed device guarantees that each blade is evenly cut through which prolongs the life of the anvil cover.
- Steel die-cutting cylinder coated with hard chrome, equipped with anvil cover from USA; automatic transverse in axial direction (±20mm), automatic speed tracking of die-board in circumferential direction, thus prolongs anvil cover lifespan and improves die-cutting accuracy.
- Diamond spiral roller grinding device which can be quantified grinding, extend the life of rubber pad and exhaust waste caused by uneven abrasion.
- Hard chrome coated and surface ground steel die-cutting cylinder, equipped with swivel nut and automatic positioning for die mounting.
- Equipped with motorized belt waste removal device.
- Pneumatic locking with slotting unit, and it can be separated apart by 1000mm, easy for maintenance and blade change.
- Die-cutting accuracy: ±1.0mm
Stripping unit
- Intensive rollers structure, realized function of vibrating, conveying in wave shape when there is tiny warp, and accurate sheet transfer.
- Pneumatic opening of conveying passway, convenient for maintenance and cleaning.
- Equipped with waste removal fan.
- Equipped with lateral waste removal device.
Folder Gluer
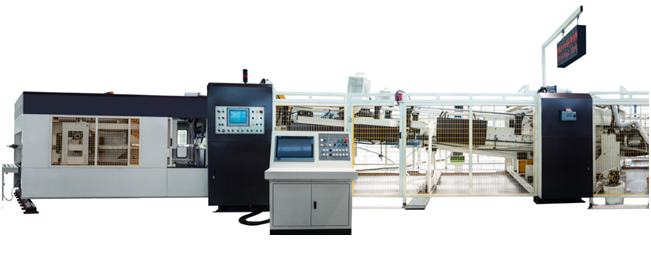
- International famous brand extrusion system, European ERO-OS.
- Automatic adjustment of glue quantity based on sheet speed.
- Automatic adjustment of glue line length based on sheet specification.
- Automatic adjustment of extrusion position based on sheet specification.
- Three-nozzle gun is standard. Two-nozzle gun is recommended in case of the glue overlap is less than 30mm and four-nozzle gun is recommended in case of the glue overlap is more than 40mm.
2. Folding unit:
- Motorized brush wheel and high-pressure blower to remove corner-cutting scraps.
- Vacuum belt transfer with less wear and high feeding accuracy.
- Automatic air cylinder adjustment for belt tension control, automatic belt loosening when power off prolongs belt lifespan.
- Synchronous transfer of top and bottom high friction needle belt in front section ensures square feeding.
- Auxiliary folding wheel for 2nd time creasing, ensures better formation for 5 ply carton.
- Folding wheels in rear section effectively control sheet folding process and avoid fishtail.
- Accurate speed differential adjustment for top and bottom folding belts reduces scissors error when the carton is formed.
- Motorized folding beam movement for different carton sizes demand
3. Drive unit
- Variable frequency motor driven, synchronizing with printer
- USA Gates timing belt ensures accurate transfer and low noise.
- Out-feeding roller for folded carton pressing, ensuring well bonding. The top out-feeding rollers are rubberized and steel is for the bottom rollers. Conveying gap between top and bottom rollers is motorized with digital readout.
- High-speed jogging system for final carton correction and squaring.
4 Counting and ejecting unit
This part realizes high-speed counting and ejecting, and mainly consists of collecting unit, auxiliary collecting unit, collecting table and pushing mechanism.
- Accurate sheets counting with photocell
- Servo motor controls collecting bracket and batching table for accurate sheet batching. Closed-loop control for servo system, ensuring accuracy and lower impact force
- 10~25 sheets per bundle can be pre-set.(Speed/sheets per bundle curve for reference)
- Auxiliary collecting unit ensures enough buffering time for batching at high speed
- Servo driven for conveying rollers and synchronizing with sheet pressing device, brings neat sheets stacking at exit.
- Strong force blower avoids the sheets up-warp, flow direction can be adjusted and flow rate is controlled via variable frequency.
- Rubber cushion is assembled to the backstop, reducing the impact to the carton edge and avoiding damage.
5. Ejecting unit
- Upper ejecting unit can be adjusted front and back with the backstop
- Motorized adjustment of height direction position of upper ejecting unit through lifting device. Upper ejecting unit height adjustment ranges from 100mm to 340mm according to the sheets per bundle.
- Synchronous drive belt for upper and lower ejecting unit without stacking jam.
- Whole ejecting unit can be adjusted left and right to keep the bundle located in the middle of machine
Glue extrusion system
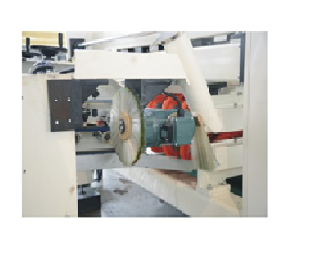
- International famous brand extrusion system, European ERO-OS.
- Automatic adjustment of glue quantity based on sheet speed.
- Automatic adjustment of glue line length based on sheet specification.
- Automatic adjustment of extrusion position based on sheet specification.
- Three-nozzle gun is standard. Two-nozzle gun is recommended in case of the glue overlap is less than 30mm and four-nozzle gun is recommended in case of the glue overlap is more than 40mm.
Folder Gluer-II
- Drive unit
- Variable frequency motor driven, synchronizing with printer
- USA Gates timing belt ensures accurate transfer and low noise.
- Out-feeding roller for folded carton pressing, ensuring well bonding. The top out-feeding rollers are rubberized and steel is for the bottom rollers. Conveying gap between top and bottom rollers is motorized with digital readout.
- High-speed jogging system for final carton correction and squaring.
- Counting and ejecting unit
- This part realizes high-speed counting and ejecting, and mainly consists of collecting unit, auxiliary collecting unit, collecting table and pushing mechanism.
- Accurate sheets counting with photocell
- Servo motor controls collecting bracket and batching table for accurate sheet batching. Closed-loop control for servo system, ensuring accuracy and lower impact force
- 10~25 sheets per bundle can be pre-set.(Speed/sheets per bundle curve for reference)
- Auxiliary collecting unit ensures enough buffering time for batching at high speed
- Servo driven for conveying rollers and synchronizing with sheet pressing device, brings neat sheets stacking at exit.
- Strong force blower avoids the sheets up-warp, flow direction can be adjusted and flow rate is controlled via variable frequency.
- Rubber cushion is assembled to the backstop, reducing the impact to the carton edge and avoiding damage.
- Ejecting unit
- Upper ejecting unit can be adjusted front and back with the backstop
- Motorized adjustment of height direction position of upper ejecting unit through lifting device. Upper ejecting unit height adjustment ranges from 100mm to 340mm according to the sheets per bundle.
- Synchronous drive belt for upper and lower ejecting unit without stacking jam.
- Whole ejecting unit can be adjusted left and right to keep the bundle located in the middle of machine